
There is a function to return all locos to their "home" (starting point) when you have finished. If you want to add individual loco or even rolling stock detection you can do that as well with barcodes or RFID but there is no need. It uses a block structure and once you place a loco in a block it always knowns where it is via block sensors. Rocrail was designed with automation in mind. I have no vested interest in it, just a satisfied user. This is what I know about Rocrail from my experience. It supports a variety of sensors, see here: sensors It supports DCC++ on Arduino, see here: dccpp:dccpp-en To continue my earlier comments on Rocrail. What I don’t know is how any of them would interface with your Arduino interface.
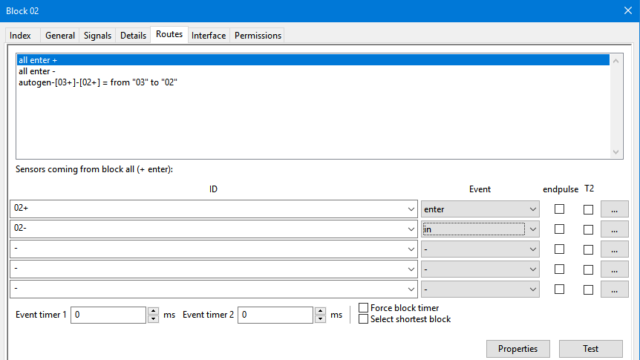
#Rocrail software trial
A free trial is available, so you can try all of them without any up front investment. Not sure if any of that is helpful! I have no hesitation in recommending iTrain. There is also Train Controller - don’t know much about it. I barely scratch the surface of what it can do. It is very stable, very reliable and very capable.
#Rocrail software software
ITrain is commercial software which you pay for - it’s development is very active and in the past ten years has continued to add new functionality. I think it has a similar feature set to iTrain. JMRI PanelPro wasn’t what I was looking for, Rocrail was much closer, but iTrain’s UI was what really sold it to me.Īs I understand it Rocrail is open source and free. I looked at Rocrail and JMRI when I was starting. ITrain supports many commercially available command stations and can support more than one if needed. I use a Lenz command station and a USB interface. You are right that a DCC command station handles commands to the layout as well as feedbacks from the layout, and therefore has a single data connection to a computer. I’ve been using iTrain for ten years and like it very much. ITrain - I know nothing about this one, from what i have read it is very similar to Rocrail with very similar automation possibilities? I need to establish the same feedback requirements. What i need to establish, will Rocrail recognise my Arduino sensor shield as an independent USB input to the computer or does feedback need to come through the controller? What i liked is the almost immediate suggestion that automation was not only possible but built in from day 1. Rocrail - I have set up Rocrail and am quite impressed but so far I have only used the intro section and not connected to my DCC controller. Also feedback from my existing Hall sensors via an Arduino is possible (I understand) as JMRI will find the incoming port?
#Rocrail software pro
JMRI - I understand this works well with Arduino however I have problems running it on my oldish MAC computer ( Catalina ) Decoder Pro works but Panel Pro refuses to start? Assuming I can make it work on a MAC i believe automation is possible but requires Python type programming. I would prefer to use Arduino type units rather than buy commercial products partly because its more interesting and also because it can take up to 6 weeks for parcels to arrive here and a proportion inevitably get lost.
#Rocrail software manual
The manual is essentially used when something goes wrong and i need to bring things back to the correct starting point. I will probably run like today with 80+ % automatic operation.
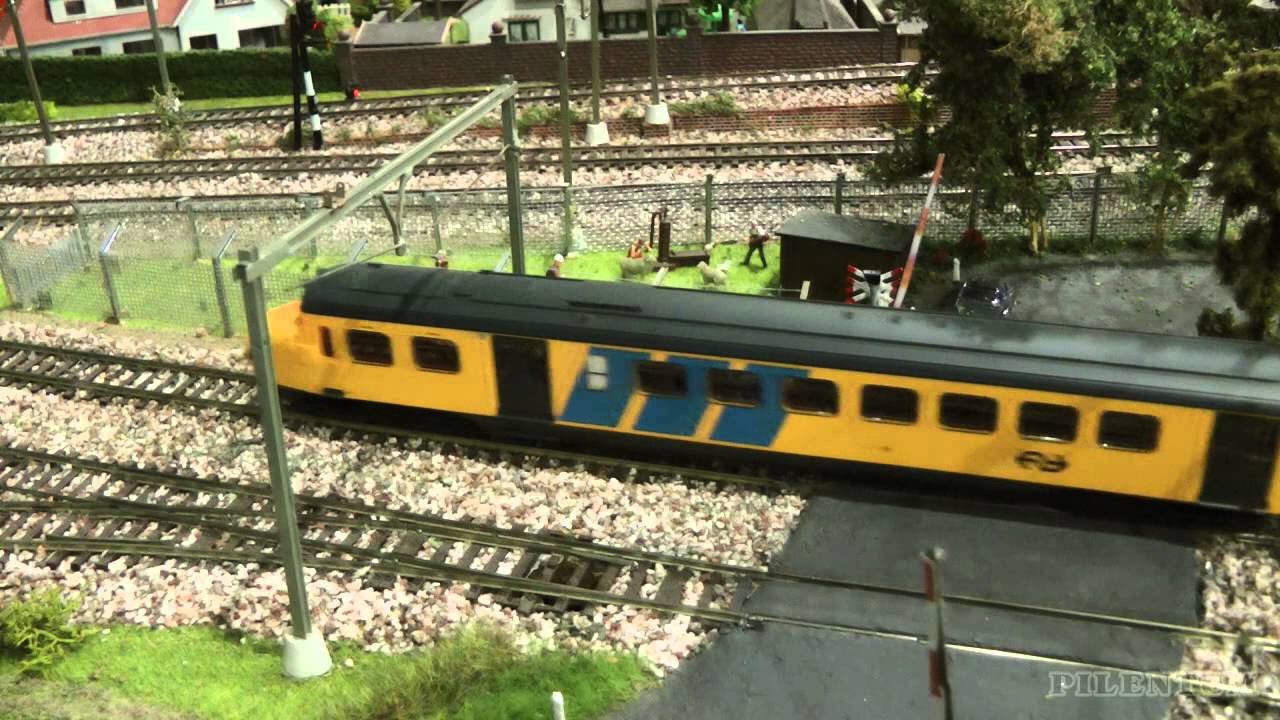
I now need some sort of control interface and would like some advice.
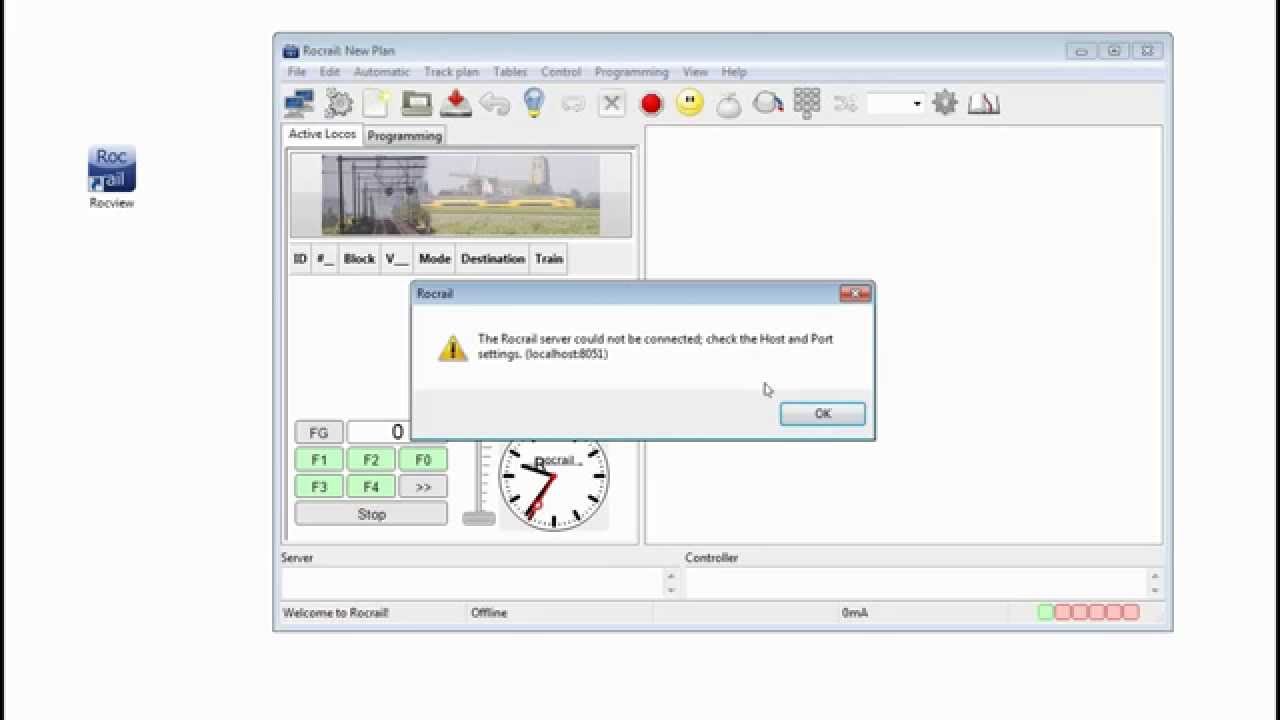
I am starting to experiment with DCC, I have a DCC controller made with an Arduino Uno and motor shield running DCC++EX which works well. In principle this can be corrected by programming but as I am required by higher management to "put my crap away after use" I have to make a set up each time i run the layout and the set up must always be the same, a system which can recognise the engine could be better. This setup runs very well and does not need a JMRI type of interface, however there are some limitations, the fast express, the commuter DMU and the freight train run at approximately the same speed as the Arduino cannot identify an engine. The automatics are DC and controlled by Arduinos, position sensing by Hall effect switches and with magnets under the engines. I have a small n gauge layout in 4 parts, one fully automatic branch line, two mainline tracks with independent fiddle yards which can be either fully automatic or manual and a central shunting yard which is fully manual including an Arduino controlled turntable.
